Materials
Pressure Sensitive Labels
For cans and bottles, typically we choose between Paper or BOPP (biaxially orientated poly-propylene) materials for our pressure sensitive labels.
Paper
- Not used a lot for food/beverage (because of condensation)
- Laminates can be applied to mitigate the effects of condensation
- Tends to be cheaper
Two Primary Paper Options:
A standard for non-food/beverage, this is paper with a thin coating
Use when you want both metallic elements as well as haptic effects (similar to embossing)
BOPP
- Used more often than paper
- Can use laminates or varnishes to protect ink or create texture on label
- More versatile
Three Primary BOPP Options:
Just white; all colors “pop” on white
Crystal clear that can show both shiny finish of the can underneath as well as opaque areas with printed white underneath
The material is silver and can be tinted any color; similar to clear, to achieve opaque colors and elements, white can be laid down first in sections
Finishes
Matte: Satisfyingly non-glossy all over varnish or laminate
Gloss: High gloss all over shine
Features
Foiling: Foil or silver ink on only specific areas of a label
UV Ink: Works great for hidden messages or promotions, this ink can only be revealed under a black light
Fluorescent Pink Ink: Creates a special kind of pop on labels, also impressive under a black light

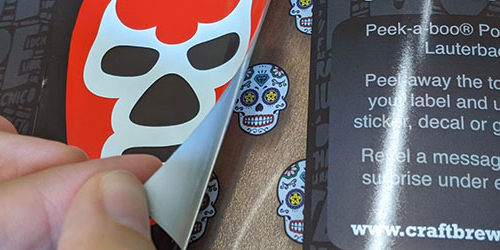
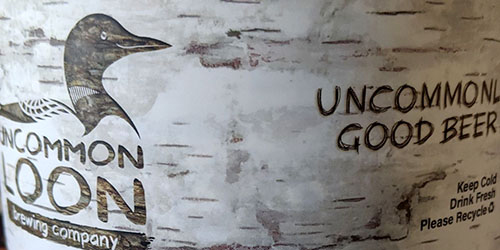
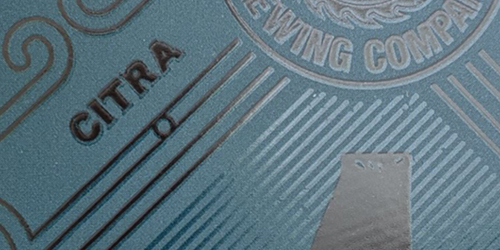
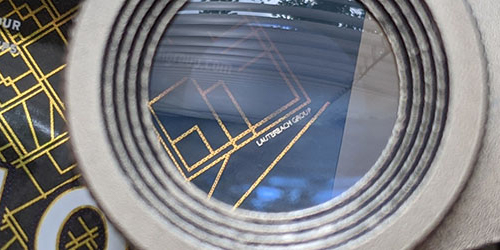
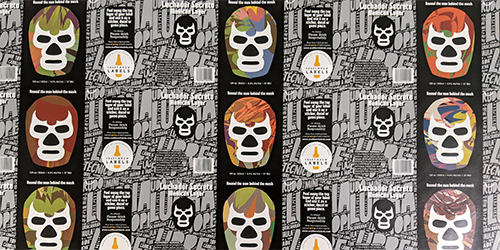
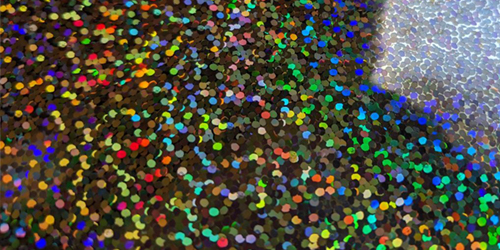
Shrink Sleeves
Technically we have produced both PVC (Polyvinyl chloride) and PET (Polyethylene Terephthalate) shrink sleeves, however recycling regulations and the plastic industry direction are moving away from PVC and towards PET because of recyclability. The chloride portion of PVC can be released as harmful chlorine or HCl gas in certain recycling or disposal methods.
Finishes
Matte: Non-glossy all over varnish
Gloss: Standard gloss all over shine
Features
Fluorescent Pink Ink